Airflux, air comprimé, azote et eau glacée : quelles pistes d’optimisation énergétique ?
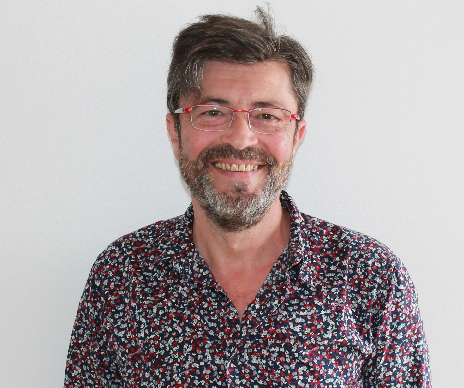
Rouen : 100 000 €/an d’économies grâce à la récupération de chaleur sur le compresseur.
Francis Lopez, Directeur Ventes & Marketing chez Airflux
« Un audit pour quantifier les besoins du client et apporter des solutions adaptées. »
Dans le domaine agroalimentaire, les productions d’air comprimé industriel, d’azote et d’eau glacée ouvrent de belles perspectives en termes d’optimisation énergétique, tout en intégrant des contraintes de performance. Que ce soit à partir de gaz ou d’électricité, générer un autre média (eau glacée, vapeur, air comprimé etc …) est excessivement coûteux, et ne cesse d’évoluer impactant la productivité des industriels.
L’intérêt est notamment de combiner les utilités, grâce à des transferts de calories, comme l’évoque Francis Lopez, Directeur Ventes & Marketing chez Airflux.
Quelles sont les attentes de vos clients travaillant dans le secteur agroalimentaire ?
Elles sont multiples. Il y a, tout d’abord, la recherche de réduction des consommations d’énergie, ce à quoi nous apportons des réponses depuis longtemps : nous avons été les premiers à équiper nos compresseurs d’air de systèmes de récupération de chaleur dans les années 2000 . Rappelons que 94 % de la puissance électrique consommée par un compresseur se dissipe sous forme de chaleur. Or, il est possible de mobiliser ces calories. Nous avons ainsi le cas d’un industriel qui récupère la chaleur fatale issue de la compression pour chauffer ses bâtiments avec, à la clé, une réduction de 60 % de sa facture de chauffage. Dans la région lyonnaise, un autre industriel récupère l’énergie issue de la production glacée pour assurer le maintien en température d’une cuve de process. Ce transfert de calories présente un retour sur investissement de 3 ans, sans même intégrer l’inflation des prix de l’énergie.
En réduisant les consommations d’énergie, votre secteur d’activité peut aussi décarboner les process de production…
Tout à fait : sur un site proche de Rouen, le chauffage des bâtiments, grâce à la récupération de chaleur sur la compression d’air, a non seulement généré 100 000 € d’économies annuelles, mais aussi l’évitement de 600 t de CO2 par an. Sur ce site, la démarche RSE visait également à améliorer le cadre de travail des collaborateurs, à travers la réduction du niveau sonore des machines. Dans d’autres cas nous pouvons même aller jusqu’à effacer 90 % de la consommation de gaz sur des chaudières par ce type de solutions.
Comment procède-t-on pour engager une démarche d’optimisation d’un site industriel ?
Le premier pas vers l’efficience est la recherche de sobriété. Cela passe par un audit énergétique qui permet de prendre une photo de l’usine à l’instant t et d’identifier ainsi les gaspillages et les gisements d’optimisation. Par exemple, on observe les habitudes de travail en matière de températures ou de pressions pour les baisser, si possible. Ensuite, un ensemble de mesures sur les installations permettent de quantifier les besoins du client et d’apporter des solutions adaptées pour réduire les consommations. Cela peut être des compresseurs à vitesse variable ou à haute pression flottante, des groupes froids spécifiques… Après la sobriété, vient l’efficacité avec la possibilité, comme nous l’avons déjà évoqué, de mobiliser la chaleur fatale, grâce à des échangeurs à plaques pouvant récupérer jusqu’à 72 % des calories. Ensuite, les consommations restantes peuvent être couvertes par des énergies renouvelables. Nous développons ainsi une solution de micro-génération d’électricité à partir d’eau chaude.
L’optimisation énergétique peut-elle accompagner la performance globale de la production ?
Oui : nous gardons à l’esprit que pour un industriel, la fiabilité des installations reste la première des priorités. Il est ainsi possible d’intégrer au récupérateur de chaleur un système de gestion de l’énergie et un superviseur web dans une optique d’industrie 4.0. Ce monitoring permet un pilotage optimisé de l’énergie récupérée, ainsi qu’une amélioration des installations, à travers la détection de dérives de consommations. Nous avons l’exemple d’une usine qui, dans le cadre d’un réaménagement, avait installé une source de chaleur à proximité de compresseurs. Ceux-ci avaient, dès lors, vu leur rendement diminuer. Cet exemple souligne toute l’importance de connaître le fonctionnement d’une usine à l’instant.