« L’utilisation de béton recyclé est déjà bien avancée en Belgique ou aux Pays-Bas »
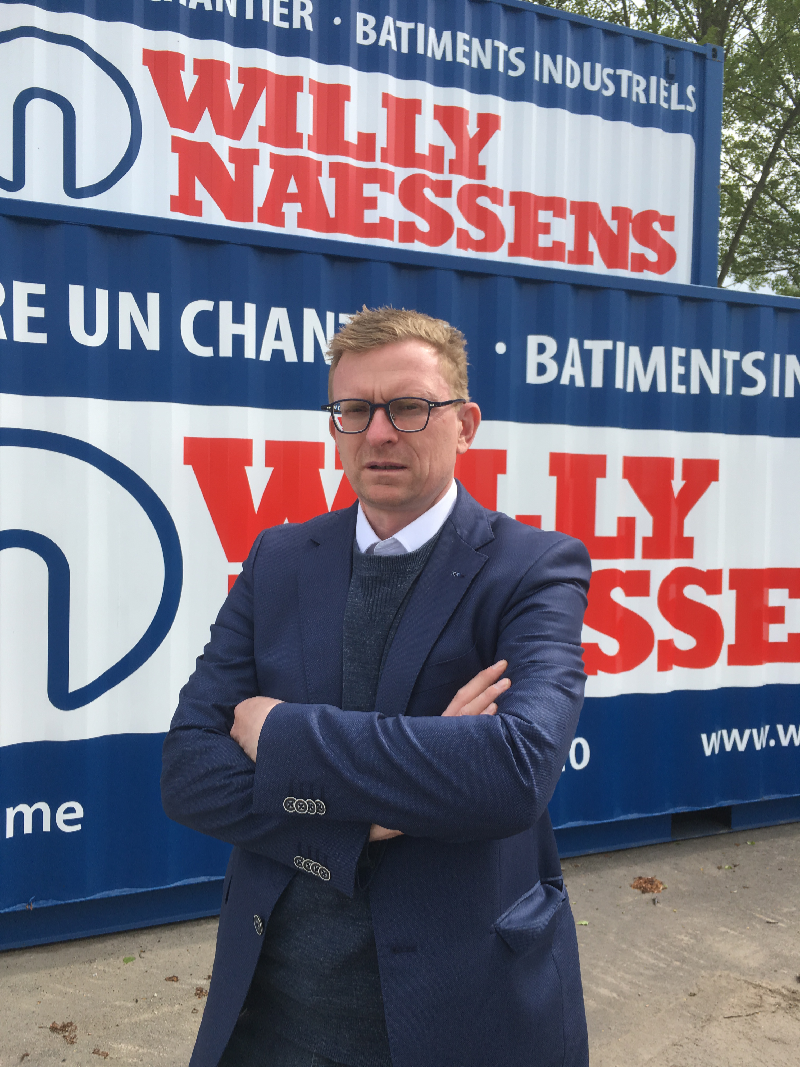
Béton et empreinte carbone des bâtiments industriels
Une optimisation des consommations énergétiques, grâce à une forte inertie thermique
Bert Noterman,
Directeur Général
Willy Naessens France Nord
Doté d’une forte inertie thermique, le béton assure une température constante dans le bâtiment avec, à la clé, moins de chauffage en hiver et de climatisation en été. Des performances qui peuvent encore être poussées, grâce aux panneaux en béton isolé. Et si la fabrication de ce matériau est consommatrice d’énergie, celle-ci pèse finalement peu au regard de la durabilité dans le temps des bâtiments en béton. Le point avec Bert Noterman, DG Willy Naessens France Nord.
Comment le béton peut-il contribuer à réduire l’empreinte carbone d’un bâtiment industriel ?
Avec sa forte inertie thermique, il permet de limiter les déperditions thermiques, d’optimiser la récupération des apports solaires, le jour, ou encore d’emmagasiner de la fraîcheur, la nuit. Ces performances thermiques peuvent encore être renforcées avec l’utilisation de panneaux de façade bilames, avec un noyau d’isolant placé entre deux couches de béton. De tels panneaux atteignent des niveaux d’isolation avec une résistance thermique R supérieure à 6 m²K/W. Des joints isolants entre les panneaux empêchent aussi la formation de ponts thermiques, tout en assurant l’étanchéité à l’air. Et pour avoir une approche globale de l’enveloppe, il existe aussi des solutions en éléments béton pour les toitures. En termes de réduction d’empreinte environnementale, rappelons aussi que le béton est un matériau durable dans le temps.
Cette longévité permet-elle « d’amortir » les consommations d’énergie et les émissions de carbone liées à la fabrication du béton ?
Tout à fait. Sans compter que, depuis le 1er janvier dernier, toutes nos nouvelles activités de fabrication sont certifiées neutres en carbone, grâce à la mobilisation des énergies renouvelables et à une politique de compensation. Nous maximisons aussi l’utilisation de produits naturels peu agressifs pour nos personnels et pour l’environnement. Par exemple, nous utilisons une huile de décoffrage bio sans solvants. Tous ces engagements nous permettent de répondre aux attentes de nos clients, de plus en plus consciencieux au sujet de l’environnement. Sur ce point, nous gardons à l’esprit qu’en termes de fabrication, le point faible du béton réside dans la part d’énergie nécessaire à la production du ciment. La préfabrication en usine de nos éléments en béton permet justement d’optimiser les mélanges de ciment. Elle permet aussi de recycler les surplus de béton et d’eau issus des process.
En parlant de recyclage, le béton peut-il s’inscrire dans une économie circulaire, à travers sa réutilisation ?
C’est déjà le cas avec l’utilisation de granulats issus de béton recyclé. Il s’agit là d’un sujet déjà bien avancé en Belgique ou aux Pays-Bas. Actuellement, nous menons un travail de R&D pour accroître toujours plus la part de ces granulats dans les bétons. En fonction de la nature du béton recyclé et des usages qui en sont faits, nous pensons pouvoir atteindre jusqu’à 30 % de granulats pour du béton maigre, non destiné à des applications non structurelles. Et comme le transport constitue une part importante des émissions de carbone liées à la construction, nous menons aussi des recherches pour permettre le recyclage de béton à la source. En parallèle, rappelons que les pistes d’optimisation environnementale de nos métiers sont, avant tout, liées à l’optimisation technique de chaque projet.
Comment cela ?
Nous avons déjà évoqué la préfabrication en usine, mais avant cela, la phase d’études et de dimensionnement des constructions permet d’optimiser les coffrages, les poutres, les quantités de béton utilisées, etc. Il y a donc à la fois des gains sur la production et sur le transport. Cette approche globale est d’autant plus facile quand on maîtrise, de façon verticale, l’ensemble de la chaîne de la construction, depuis les études jusqu’à la réalisation du chantier. Et comme nos 13 sites de production des éléments préfabriqués font plus de 1500 m3 de béton par jour, l’optimisation peut aussi se faire sur les volumes…
Plus d’info https://www.willynaessens.fr/